旋挖钻机在大直径特长桩施工中应用
2018-11-11 9:43:58 点击:
在土质地区,旋挖钻机施工已广泛应用于桩基施工中,旋挖钻机成孔不但成本低,速度快,而且成孔质量高。基本没有沉碴或沉碴很少。特别是大直径桩基,通过对旋挖钻机成孔技术的研究,更好的掌握旋挖钻机成孔技术及要求,可广泛应用于大直径特长桩施工。
1.1工程概况
本工程某大桥全长6537.375m,主墩基础设计为钻孔桩,直径2.0m,桩长分别为46.5m、45.5m。
1#墩桩长为从原地面下54.586m,地质情况为:原地面以下13.3m为流塑状褐黄色淤泥质粉质粘土,基本承载力为60kpa,13.3m~22.16m为灰绿色粘土,基本承载力为180kpa,22.16m~39.86m为褐黄色粘土,基本承载力为220kpa,39.86m~43.16m为灰白色全风化泥质粉砂岩,基本承载力为250kpa,43.16m~54.586m为砖红色弱风化泥质粉砂,基本承载力为400kpa。
2#墩桩长为从原地面下52.586m,地质情况为:原地面以下32.3m为灰绿色粘土,基本承载力为180kpa;32.3m~48.3m为褐黄色粘土,基本承载力为220kpa,48.3m~51m为灰白色全风化泥质粉砂岩,基本承载力为250kpa,51m~52.586m为砖红色弱风化泥质粉砂,基本承载力为400kpa。
1.2施工方案比选
1.2.1方案一:采用冲击钻施工
根据地质资料显示,冲击钻也可以成孔,但其存在两个缺点,第一:施工周期较长,由于1#、2#为跨运河主墩,均处在运河河边,与运河防洪大堤紧邻,施工场地较狭小,每个墩最多能容纳2台冲击钻同时施工。正常情况下一台冲击钻成桩需7个工作日,则每个墩桩基施工需70个工作日,也增加了施工的安全隐患。第二:冲击钻施工成本较高,平均每米单价约为400元。
1.2.2方案二:旋挖钻机成孔
旋挖钻机有成桩速度快,施工成本低等显著特点,但对地质条件也有较高要求。一般适合于土质地层,对地基承载力也有一定的要求,一般情况下大于500kpa,但对小于80kpa的软土底层使用旋挖钻机也很容易塌孔甚至存在埋钻危险。本桥2#墩地质情况完全符合旋挖钻施工要求,但是对钻机选型上要特别考虑,需能满足开挖承载力为400kpa的弱风化泥质粉砂地段。但本桥1#墩地质情况较复杂,原地面以下13.3m为流塑状褐黄色淤泥质粉质粘土,基本承载力为60kpa。如果用旋挖钻机施工容易造成塌孔。另外由于地处运河边,场地狭小,对环境保护要求也较高,护壁用的泥浆循环和排放也需妥善处理。桩基底部深达11.3m的弱风化泥质岩旋挖钻机能否顺利开挖也需谨慎考虑。
根据对冲击钻和旋挖钻机施工特点的比选,虽然使用旋挖钻机施工有需要解决的问题,但通过一定的方案优化可以很好的解决这些问题,而且旋挖钻机施工有明显的施工速度快、工期短、成本低等特点,故可采用旋挖钻机作为桩基施工机具。
1.3施工工艺
1.3.1旋挖钻机类型选择
根据桩基设计孔径和桩基长度,选用徐工XR250C旋挖钻机施工,其主要技术参数为:
A、最大输出扭矩:250KN.m;B、钻孔转速:7-26/128rpm;
C、最大加压力:180KN;D、最大起拔力:240KN;
E、钻机安全角度:100;F、主卷扬钢丝绳直径:2800;
G、主卷扬提升速度:70m/min;H、最大成孔深度:67m;
I、最大钻孔直径2300(2500)mm;J、工作状态高度:21045mm
K、最大总质量:70t。
1.3.2施工场地平整
旋挖钻机总质量达70t,且工作时高度达21m,若不对工作平台进行压实处理,很容易发生安全事故。工作平台尺寸至少比承台顶面尺寸各大2m,1#、2#墩工作平台尺寸为20.2*16.3m。将此范围内的表层50cm粘土换填成碎石土,进行推平碾压。待碾压好后进行轻型动力触探试验,满足35锤及以上(承载力达到200kpa)要求方能上旋挖钻机。
1.3.3钻孔作业平台
2#墩部分桩基位于河内,桩基施工前需搭设钻孔平台。平台采用Φ500钢管作为桩基钢管桩,顺桥向间距为3.5m,横桥向间距为3.2m。钢管桩之间采用剪刀撑加强稳定连接。梁采用I32b工字钢,梁上铺设厚20mm的钢板作为工作平台。
1.3.4钢护筒制作
钻孔桩钢护筒采用壁厚10mm的钢板制作,内径为2.4m。采用挖埋的方法沉设钢护筒,护筒深度根据桩顶土质情况决定,其中1#墩由于桩顶位于淤泥质粉质粘土中,承载力较低,容易发生塌孔现象,需加长钢护筒。根据地质情况显示及在施工中采用相应措施,采用4m长钢护筒即可。2#墩水中部分桩基钢护筒长5m,以深入河床以下1m为准。钢护筒在距离顶部30cm处用直径20mm圆钢焊接“耳环”做吊点,便于拔出钢护筒。
1.3.5钻进施工
A钻进施工前,再次将钻头、钻杆、钢丝绳等进行全面检查。
B开始钻进时,开启钻机将钻筒中心对准设计桩位中心,先将钻头垂吊稳定后,再慢慢导正下入井孔,然后匀速下放至作业面,液压装置加压,旋转钻进,操作室内显示进尺及钻头位置,按轻压慢钻的原则缓缓钻进。钻碴通过进渣口进入钻筒,同时向孔内注入泥浆,根据屏显深度,待确定钻筒内钻碴填满后,反转后即可关闭进碴口。提升钻杆带动钻筒,同时继续向孔内注泥浆,确保孔内水头后,将钻筒提出孔外,提钻时开始要缓慢,提离孔底数米后,如未遇到阻力,方可加速按正常速度提升至井口,利用液压系统,将筒门打开,排除钻碴,如此反复,直至离设计标高剩余最后一钻即30-50cm。等待5-10分钟,待残碴沉淀后开始最后一钻,将残碴一并带出。
C成孔后,更换清底钻头,进行清底,并测定孔深。
D钻进中发现有塌孔、斜孔时及时处理。发现缩径时,经常提动钻具上下反复修扩孔壁。
E每次钻进深度以不超过0.5m为宜。
F护壁:选用现场原状土造浆,由于场地较狭小,采用泥浆循环利用原则。即在基坑外3m处开挖一泥浆池,尺寸为10×5×2m,泥浆比重1.1~1.3,钻孔桩施工时试验人员现场用NB-1泥浆比重计测定泥浆比重,合格后方可入孔。为了防止坍孔,泥浆应有一定的粘度,按照不同的土质,粘度指标见表1。
机长认真执行钻探操作规程,根据地层情况及时调整泥浆性能,保证成孔速度和质量,施工中随着孔深的增加向孔内及时、连续地补充泥浆,维持护筒内应有的水头,防止孔壁坍塌。混凝土灌注过程中,开挖泥浆沟,使孔内泥浆返回泥浆池,防止泥浆外溢。
1.3.6钻进施工控制
施工过程中可以通过钻机本身的三向垂直控制系统反复检查成孔的垂直度,确保成孔质量。该钻机最大的特点是采用液压系统,根据地质情况随意控制钻进速度。(通过低液限土层时4~6m/h,稍密细砂层时6~8m/h,中密至密实的砾卵石及砾石层8~10m/h)。
1.3.7清孔
钻机钻至设计标高后,提至孔顶,严禁出现超钻现象,进行孔深量测合格后,进行清孔。清孔采用泥浆泵换浆清孔,将新拌泥浆置换孔内泥浆,使孔内泥浆比重、粘度、含砂率等指标满足灌注水下砼的需要。钢筋笼安装到位后,进行二次清孔,二次清孔采用导管注清水将孔底泥浆冲散,使之呈悬浮状态,经测量沉碴满足要求后开始灌注水下砼。
1.3.8旋挖钻施工工艺流程
1.3.9.1淤泥质粘土地段注意事项
当旋挖钻机施钻淤泥质粉质粘土时,非常容易因承载力不足而发生塌孔现象。如1#墩的桩顶以下13m范围,先用2根长3mI20槽钢将护筒吊起在原地面,防止发生塌孔现象将护筒陷入孔内。另外施钻时要缓进慢钻,并用空钻在孔内来回旋转摩擦增加孔壁凝聚力,且泥浆比重也应适当调大至1:1.2,使之不轻易塌孔。施钻过程中现场有专人对孔壁进行观察,若发现塌孔现象应立即停钻,并及时将钻头提起,防止发生埋钻现象。
1.3.9.2弱风化泥质砂岩地段注意事项
由于旋挖钻机对地质条件的特殊要求,当进入地基承载力达到400kpa及以上的弱风泥质砂岩地段时,旋挖钻机钻进速度非常慢,甚至会出现无法进尺的情况。此时可将1.5m钻筒换成直径为1.0m的钻筒,在桩基中心反复旋转掏孔,当桩基中心被小直径钻筒掏松后再换大直径钻筒钻进取土,如此反复更换钻筒来加快进尺。
1.3.10钢筋笼安装
钢筋应符合有关规范的规定,并应满足设计文件的要求。钢筋外观要求无裂纹、起皮、锈坑、死弯及油污等。钢筋应有出厂合格证,外观检查合格后每批应按要求抽取试样,分别作拉、弯复查试验,如有一项不合格,则加倍取样,如仍有一项不合格,则该批钢筋为不合格。
钢筋笼利用拖车运至现场安装。为保证钢筋笼吊装安装时不变形,钢筋骨架在加工时设置强劲的内撑架,防止钢筋骨架在运输和就位时变形,并设置板凳平台。钢筋笼吊装时采用两吊点起吊,先把钢筋笼吊竖直后,再检查是否有弯曲变形并加以纠正。钢筋笼骨架进入孔口后,将其扶正徐徐下放,严禁摆动碰撞孔壁。当最后一道加劲筋接近孔口时,在主筋上均匀焊上6个吊环,并用6根钢丝绳把钢筋笼固定在板凳平台上,再吊起第2节钢筋笼同第一节对接,采用帮条焊接,帮条长度不小于16�、20cm,搭接接头对接焊好后再吊起钢筋笼、取掉板凳平台上的钢丝绳下放骨架,如此循环,直至把钢筋笼骨架下放至设计标高,并用型钢把钢筋笼固定定位于孔位中心。钢筋骨架的保护层,采用中心开孔、厚5cm、半径4~5cm,与桩同标号的圆形水泥砂浆垫块穿入螺旋筋上来保证,砂浆块按竖向每隔2m设一道,每一道沿圆周穿入6~8个。钢筋笼入孔后平面位置不大于10cm,地面高程偏差不大于10cm。在钢筋笼上端均匀设置吊环,用来承担钢筋笼。
1.3.11 导管安装
导管连接采用法兰连接,法兰盘加锥形活套,底节导管下端不设法兰盘。下放导管时小心操作,避免挂碰钢筋笼。导管安装长度建立复核和检查制度,避免因误装而造成漏水。混凝土浇注架用H18型钢制作,用于支撑悬吊导管,吊挂钢筋笼,上部放置混凝土漏斗。导管位于孔中央,在浇筑前,进行升降试验。导管的升降设备能力,要与全部导管充满混凝土后的总重量和摩阻力相适应,并有一定的安全储备。
导管底口至桩孔底端的间距控制在0.3m-0.5m左右,首批混凝土满足导管初次埋置深度大于1.5m。
1.3.12 灌注水下混凝土
水下混凝土施工时先灌入首批封底混凝土,首批混凝土数量要经过计算,一次性将导管埋入不少于100cm来控制砼首次数量,现场漏斗尺寸为:底部锥形高0.5m,上口尺寸为1.5m×1.5m,上部高2m,上口尺寸为1.5m×1.5m。导管内首批混凝土与泥浆用隔水栓隔开,隔水栓预先用8号铁丝悬吊在混凝土漏斗下口,当混凝土装满与隔水栓完全接触后,剪断铁丝,混凝土即在重力作用下顶着隔水栓下沉至孔底,排开泥浆,埋住导管口,完成封底。随着浇注连续进行,及时提拔导管,混凝土浇注应连续进行,不能中途停止。
在整个浇注过程中,导管在混凝土埋深以1~3m为宜。施工中指派专人负责测量导管埋置深度及管内外混凝土面的高差,及时填写水下混凝土灌注记录。利用导管内的混凝土的超压力使混凝土的浇筑面逐渐上升,灌注高度应高于设计标高1.0m左右,在灌注时不得将混凝土整斗从上面倾入漏斗内,以免导管内形成高压气囊,冲出管节间的橡胶垫而使导管漏水。
对灌注过程中的一切故障等情况均要如实记录在案。在灌注将近结束时,在孔内注入适量的水使孔内泥浆稀释,有效排出泥浆,加大导管内外的压力差,保证浇注效果。
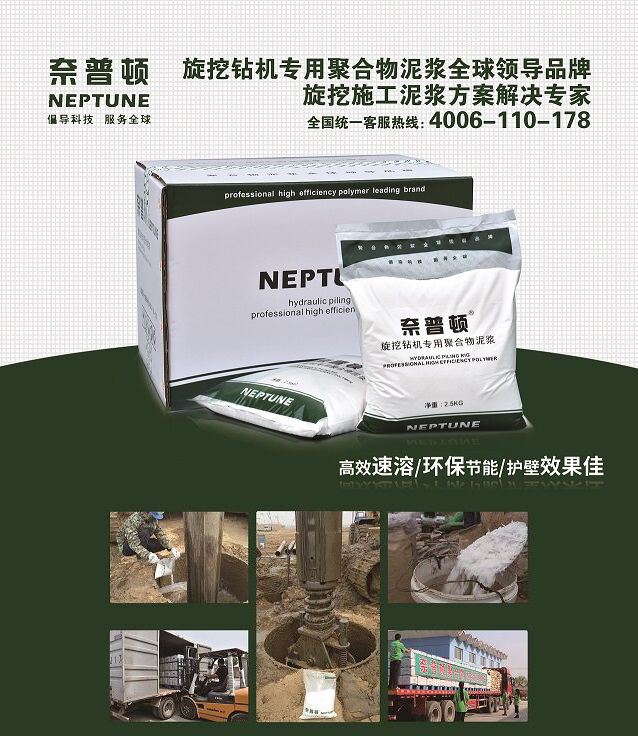
1.1工程概况
本工程某大桥全长6537.375m,主墩基础设计为钻孔桩,直径2.0m,桩长分别为46.5m、45.5m。
1#墩桩长为从原地面下54.586m,地质情况为:原地面以下13.3m为流塑状褐黄色淤泥质粉质粘土,基本承载力为60kpa,13.3m~22.16m为灰绿色粘土,基本承载力为180kpa,22.16m~39.86m为褐黄色粘土,基本承载力为220kpa,39.86m~43.16m为灰白色全风化泥质粉砂岩,基本承载力为250kpa,43.16m~54.586m为砖红色弱风化泥质粉砂,基本承载力为400kpa。
2#墩桩长为从原地面下52.586m,地质情况为:原地面以下32.3m为灰绿色粘土,基本承载力为180kpa;32.3m~48.3m为褐黄色粘土,基本承载力为220kpa,48.3m~51m为灰白色全风化泥质粉砂岩,基本承载力为250kpa,51m~52.586m为砖红色弱风化泥质粉砂,基本承载力为400kpa。
1.2施工方案比选
1.2.1方案一:采用冲击钻施工
根据地质资料显示,冲击钻也可以成孔,但其存在两个缺点,第一:施工周期较长,由于1#、2#为跨运河主墩,均处在运河河边,与运河防洪大堤紧邻,施工场地较狭小,每个墩最多能容纳2台冲击钻同时施工。正常情况下一台冲击钻成桩需7个工作日,则每个墩桩基施工需70个工作日,也增加了施工的安全隐患。第二:冲击钻施工成本较高,平均每米单价约为400元。
1.2.2方案二:旋挖钻机成孔
旋挖钻机有成桩速度快,施工成本低等显著特点,但对地质条件也有较高要求。一般适合于土质地层,对地基承载力也有一定的要求,一般情况下大于500kpa,但对小于80kpa的软土底层使用旋挖钻机也很容易塌孔甚至存在埋钻危险。本桥2#墩地质情况完全符合旋挖钻施工要求,但是对钻机选型上要特别考虑,需能满足开挖承载力为400kpa的弱风化泥质粉砂地段。但本桥1#墩地质情况较复杂,原地面以下13.3m为流塑状褐黄色淤泥质粉质粘土,基本承载力为60kpa。如果用旋挖钻机施工容易造成塌孔。另外由于地处运河边,场地狭小,对环境保护要求也较高,护壁用的泥浆循环和排放也需妥善处理。桩基底部深达11.3m的弱风化泥质岩旋挖钻机能否顺利开挖也需谨慎考虑。
根据对冲击钻和旋挖钻机施工特点的比选,虽然使用旋挖钻机施工有需要解决的问题,但通过一定的方案优化可以很好的解决这些问题,而且旋挖钻机施工有明显的施工速度快、工期短、成本低等特点,故可采用旋挖钻机作为桩基施工机具。
1.3施工工艺
1.3.1旋挖钻机类型选择
根据桩基设计孔径和桩基长度,选用徐工XR250C旋挖钻机施工,其主要技术参数为:
A、最大输出扭矩:250KN.m;B、钻孔转速:7-26/128rpm;
C、最大加压力:180KN;D、最大起拔力:240KN;
E、钻机安全角度:100;F、主卷扬钢丝绳直径:2800;
G、主卷扬提升速度:70m/min;H、最大成孔深度:67m;
I、最大钻孔直径2300(2500)mm;J、工作状态高度:21045mm
K、最大总质量:70t。
1.3.2施工场地平整
旋挖钻机总质量达70t,且工作时高度达21m,若不对工作平台进行压实处理,很容易发生安全事故。工作平台尺寸至少比承台顶面尺寸各大2m,1#、2#墩工作平台尺寸为20.2*16.3m。将此范围内的表层50cm粘土换填成碎石土,进行推平碾压。待碾压好后进行轻型动力触探试验,满足35锤及以上(承载力达到200kpa)要求方能上旋挖钻机。
1.3.3钻孔作业平台
2#墩部分桩基位于河内,桩基施工前需搭设钻孔平台。平台采用Φ500钢管作为桩基钢管桩,顺桥向间距为3.5m,横桥向间距为3.2m。钢管桩之间采用剪刀撑加强稳定连接。梁采用I32b工字钢,梁上铺设厚20mm的钢板作为工作平台。
1.3.4钢护筒制作
钻孔桩钢护筒采用壁厚10mm的钢板制作,内径为2.4m。采用挖埋的方法沉设钢护筒,护筒深度根据桩顶土质情况决定,其中1#墩由于桩顶位于淤泥质粉质粘土中,承载力较低,容易发生塌孔现象,需加长钢护筒。根据地质情况显示及在施工中采用相应措施,采用4m长钢护筒即可。2#墩水中部分桩基钢护筒长5m,以深入河床以下1m为准。钢护筒在距离顶部30cm处用直径20mm圆钢焊接“耳环”做吊点,便于拔出钢护筒。
1.3.5钻进施工
A钻进施工前,再次将钻头、钻杆、钢丝绳等进行全面检查。
B开始钻进时,开启钻机将钻筒中心对准设计桩位中心,先将钻头垂吊稳定后,再慢慢导正下入井孔,然后匀速下放至作业面,液压装置加压,旋转钻进,操作室内显示进尺及钻头位置,按轻压慢钻的原则缓缓钻进。钻碴通过进渣口进入钻筒,同时向孔内注入泥浆,根据屏显深度,待确定钻筒内钻碴填满后,反转后即可关闭进碴口。提升钻杆带动钻筒,同时继续向孔内注泥浆,确保孔内水头后,将钻筒提出孔外,提钻时开始要缓慢,提离孔底数米后,如未遇到阻力,方可加速按正常速度提升至井口,利用液压系统,将筒门打开,排除钻碴,如此反复,直至离设计标高剩余最后一钻即30-50cm。等待5-10分钟,待残碴沉淀后开始最后一钻,将残碴一并带出。
C成孔后,更换清底钻头,进行清底,并测定孔深。
D钻进中发现有塌孔、斜孔时及时处理。发现缩径时,经常提动钻具上下反复修扩孔壁。
E每次钻进深度以不超过0.5m为宜。
F护壁:选用现场原状土造浆,由于场地较狭小,采用泥浆循环利用原则。即在基坑外3m处开挖一泥浆池,尺寸为10×5×2m,泥浆比重1.1~1.3,钻孔桩施工时试验人员现场用NB-1泥浆比重计测定泥浆比重,合格后方可入孔。为了防止坍孔,泥浆应有一定的粘度,按照不同的土质,粘度指标见表1。
机长认真执行钻探操作规程,根据地层情况及时调整泥浆性能,保证成孔速度和质量,施工中随着孔深的增加向孔内及时、连续地补充泥浆,维持护筒内应有的水头,防止孔壁坍塌。混凝土灌注过程中,开挖泥浆沟,使孔内泥浆返回泥浆池,防止泥浆外溢。
1.3.6钻进施工控制
施工过程中可以通过钻机本身的三向垂直控制系统反复检查成孔的垂直度,确保成孔质量。该钻机最大的特点是采用液压系统,根据地质情况随意控制钻进速度。(通过低液限土层时4~6m/h,稍密细砂层时6~8m/h,中密至密实的砾卵石及砾石层8~10m/h)。
1.3.7清孔
钻机钻至设计标高后,提至孔顶,严禁出现超钻现象,进行孔深量测合格后,进行清孔。清孔采用泥浆泵换浆清孔,将新拌泥浆置换孔内泥浆,使孔内泥浆比重、粘度、含砂率等指标满足灌注水下砼的需要。钢筋笼安装到位后,进行二次清孔,二次清孔采用导管注清水将孔底泥浆冲散,使之呈悬浮状态,经测量沉碴满足要求后开始灌注水下砼。
1.3.8旋挖钻施工工艺流程
1.3.9.1淤泥质粘土地段注意事项
当旋挖钻机施钻淤泥质粉质粘土时,非常容易因承载力不足而发生塌孔现象。如1#墩的桩顶以下13m范围,先用2根长3mI20槽钢将护筒吊起在原地面,防止发生塌孔现象将护筒陷入孔内。另外施钻时要缓进慢钻,并用空钻在孔内来回旋转摩擦增加孔壁凝聚力,且泥浆比重也应适当调大至1:1.2,使之不轻易塌孔。施钻过程中现场有专人对孔壁进行观察,若发现塌孔现象应立即停钻,并及时将钻头提起,防止发生埋钻现象。
1.3.9.2弱风化泥质砂岩地段注意事项
由于旋挖钻机对地质条件的特殊要求,当进入地基承载力达到400kpa及以上的弱风泥质砂岩地段时,旋挖钻机钻进速度非常慢,甚至会出现无法进尺的情况。此时可将1.5m钻筒换成直径为1.0m的钻筒,在桩基中心反复旋转掏孔,当桩基中心被小直径钻筒掏松后再换大直径钻筒钻进取土,如此反复更换钻筒来加快进尺。
1.3.10钢筋笼安装
钢筋应符合有关规范的规定,并应满足设计文件的要求。钢筋外观要求无裂纹、起皮、锈坑、死弯及油污等。钢筋应有出厂合格证,外观检查合格后每批应按要求抽取试样,分别作拉、弯复查试验,如有一项不合格,则加倍取样,如仍有一项不合格,则该批钢筋为不合格。
钢筋笼利用拖车运至现场安装。为保证钢筋笼吊装安装时不变形,钢筋骨架在加工时设置强劲的内撑架,防止钢筋骨架在运输和就位时变形,并设置板凳平台。钢筋笼吊装时采用两吊点起吊,先把钢筋笼吊竖直后,再检查是否有弯曲变形并加以纠正。钢筋笼骨架进入孔口后,将其扶正徐徐下放,严禁摆动碰撞孔壁。当最后一道加劲筋接近孔口时,在主筋上均匀焊上6个吊环,并用6根钢丝绳把钢筋笼固定在板凳平台上,再吊起第2节钢筋笼同第一节对接,采用帮条焊接,帮条长度不小于16�、20cm,搭接接头对接焊好后再吊起钢筋笼、取掉板凳平台上的钢丝绳下放骨架,如此循环,直至把钢筋笼骨架下放至设计标高,并用型钢把钢筋笼固定定位于孔位中心。钢筋骨架的保护层,采用中心开孔、厚5cm、半径4~5cm,与桩同标号的圆形水泥砂浆垫块穿入螺旋筋上来保证,砂浆块按竖向每隔2m设一道,每一道沿圆周穿入6~8个。钢筋笼入孔后平面位置不大于10cm,地面高程偏差不大于10cm。在钢筋笼上端均匀设置吊环,用来承担钢筋笼。
1.3.11 导管安装
导管连接采用法兰连接,法兰盘加锥形活套,底节导管下端不设法兰盘。下放导管时小心操作,避免挂碰钢筋笼。导管安装长度建立复核和检查制度,避免因误装而造成漏水。混凝土浇注架用H18型钢制作,用于支撑悬吊导管,吊挂钢筋笼,上部放置混凝土漏斗。导管位于孔中央,在浇筑前,进行升降试验。导管的升降设备能力,要与全部导管充满混凝土后的总重量和摩阻力相适应,并有一定的安全储备。
导管底口至桩孔底端的间距控制在0.3m-0.5m左右,首批混凝土满足导管初次埋置深度大于1.5m。
1.3.12 灌注水下混凝土
水下混凝土施工时先灌入首批封底混凝土,首批混凝土数量要经过计算,一次性将导管埋入不少于100cm来控制砼首次数量,现场漏斗尺寸为:底部锥形高0.5m,上口尺寸为1.5m×1.5m,上部高2m,上口尺寸为1.5m×1.5m。导管内首批混凝土与泥浆用隔水栓隔开,隔水栓预先用8号铁丝悬吊在混凝土漏斗下口,当混凝土装满与隔水栓完全接触后,剪断铁丝,混凝土即在重力作用下顶着隔水栓下沉至孔底,排开泥浆,埋住导管口,完成封底。随着浇注连续进行,及时提拔导管,混凝土浇注应连续进行,不能中途停止。
在整个浇注过程中,导管在混凝土埋深以1~3m为宜。施工中指派专人负责测量导管埋置深度及管内外混凝土面的高差,及时填写水下混凝土灌注记录。利用导管内的混凝土的超压力使混凝土的浇筑面逐渐上升,灌注高度应高于设计标高1.0m左右,在灌注时不得将混凝土整斗从上面倾入漏斗内,以免导管内形成高压气囊,冲出管节间的橡胶垫而使导管漏水。
对灌注过程中的一切故障等情况均要如实记录在案。在灌注将近结束时,在孔内注入适量的水使孔内泥浆稀释,有效排出泥浆,加大导管内外的压力差,保证浇注效果。
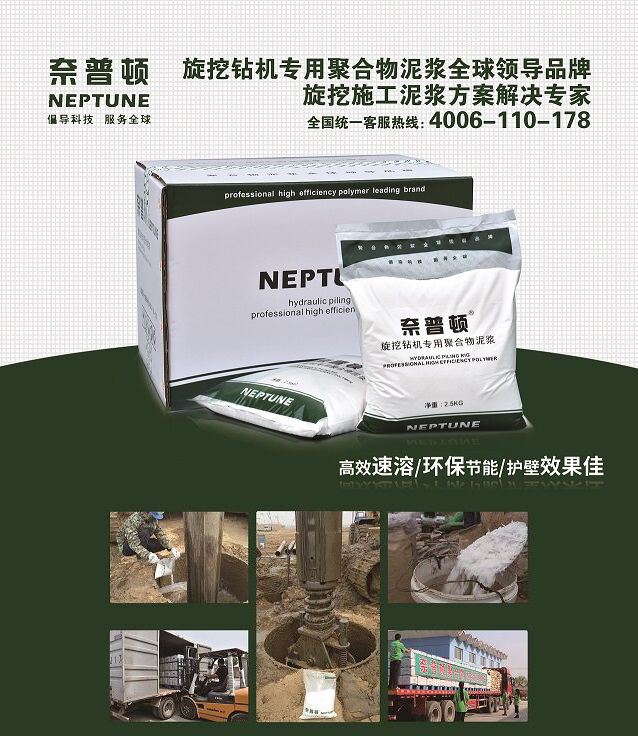
- 上一篇:旋挖孔桩桩端高压旋喷注浆处理 2018/11/11
- 下一篇:奈普顿聚合物泥浆网站新版进入调试阶段【公司新闻】 2012/5/23