广州地区旋挖灌注桩的应用分析
2018-11-9 9:28:39 点击:
近年来,随着我国经济的快速发展,工业与民用建筑、公路、铁路等工程项目不断增多,旋挖灌注桩因其效率高、适应性强、污染少,广泛应用于我国的工业与民用建筑、铁路、桥梁等大型建筑的基础桩施工。但随着应用范围的扩大,受到各类主客观因素的影响,导致各类技术问题的普遍存在,本人通过长期一线工作经验,总结出主要的两大问题,希望能引起施工单位和科研设计单位的高度重视,并积极制定有效的对策。
1、旋挖桩施工的特点
1.1成孔速度快
一般情况下,旋挖钻机的钻孔与成孔速度可以达到1-1.5m�min,与国内桩基础工程中传统的循环钻机相比,其优势极为明显。由于旋挖钻机的成孔速度快,在保证施工进度的基础上,有效减少了施工的人力、物力投入。
1.2适应性强
旋挖钻机采用液压履带式伸缩底盘、自行起落可折叠钻桅、伸缩式钻杆、带有垂直度自动检测、调整、孔深数码显示等。旋挖钻机配合不同钻具,适用于干式(短螺旋)或湿式(回转斗)及岩层(岩心钻)的成孔作业。旋挖钻机还可配挂长螺旋钻、地下连续墙抓斗、振动桩锤等,实现多功能特点,其施工效率高,是市政建设、铁路、公路桥梁、地下连续墙、水利、防渗护坡等理想的基础施工设备。旋挖钻机适用于填土层、粘土层、粉土层、淤泥层、沙土层以及短螺旋不能钻进的含有部分卵石、碎石的地层。采用岩心钻头,还可嵌入岩层。据国内机械技术部门研究,旋挖钻机的成孔速度是循环钻机的5-10倍之间。
1.3环保性能突出
国内传统循环钻机普遍采用连接钻杆与掏渣桶掏渣的泥浆循环方式,在施工现场必须设置一定容积的泥浆池,从而难以保证文明施工。而现阶段使用的旋挖钻机则是采用动力头的循环形式,其基本工作原理为:使用螺旋钻头与旋挖斗,通过强大的扭矩将土、砂砾等钻进中产生的钻渣直接进行旋挖挖掘,并快速提至孔外。由此可见,旋挖桩在施工中无需设置泥浆支护结构,实现了较为环保的干法施工,必然使施工作业过程的污染源明显减少,有利于改善施工现场的作业环境。
2 旋挖桩施工工艺流程
旋挖桩的施工工艺流程为:场地平整→孔位测定→埋设护筒→钻机就位→开钻成孔→提钻清空→检孔→安放钢筋笼→下导管→水下混凝土灌注→提拔导管→成桩→拔出护筒→检测。
3 旋挖桩施工出现的主要问题
3.1嵌岩能力差
旋挖钻机施工原理是利用可以伸缩的旋式钻杆在钻具重量、油缸压力及动力头扭矩的共同作用下,钻机自动定位,垂直旋孔,将地下土、岩屑装入钻头(筒),再用卷扬机提升取土(岩)成孔。配合不同钻具,可用于不同孔径及地质条件的成孔作业。这就决定了如果遇到硬度较大的基岩时,钻进难度就会明显加大。
广州某部队办公指挥大楼桩基础施工,根据勘察资料,该地区基岩为燕山期花岗岩。场地中风化岩面埋深32.9~45.2m,平均37.8m;层厚0.0~2.2m,平均1.2m;取岩样饱和单轴抗压强度范围值为7.38~39.6MPa,平均值为18.7MPa。下覆微风化花岗岩饱和单轴抗压强度范围值为42.2~86.5MPa,平均值为68.1MPa。设计要求桩入中/微风化岩0.5m。在桩的成孔方式上,相关单位考虑到工期及环保因素,决定采用旋挖桩成孔。试桩时,约用时1小时便穿过上部约35m厚的土层,在遇到硬度相对较大的中风化花岗岩时,钻进速度极剧下降,表现出明显的钻进困难。经多次反复旋挖,仍然没用明显的钻进效果。最终不得不停止旋挖,改用钻桩机成孔,造成了一定的经济损失并延误了工期。
广州地区基岩多为花岗岩和红层(泥质粉砂岩、粉砂质泥岩、泥岩等),在桩基础的选择上,相关单位应充分考虑到基岩的强度。如果采用嵌岩桩,在较硬的花岗岩地区,不建议采用旋挖桩;在较软的红层地区,则可采用旋挖桩,成孔速度较理想。
3.2桩底沉渣厚度大
当钻孔到达设计桩长以及进入持力层规定深度后,直接利用钻具进行换浆清孔工作,利用钻头叶片的搅动作用和泥浆对沉渣的浮力,将孔底沉渣排出孔外。清孔时应另行输入比重在1.1g/cm3以下的经沉淀除渣后较洁净的泥浆吗,逐步置换出孔内较粘稠、含较多泥砂的泥浆,而不直接输入清水,以防止发生孔壁坍塌。清孔后孔底500mm以内泥浆比重应小于1.25,含砂率不大于8%,粘度不大于28s。第一次清孔是能否达到技术要求的根本基础,第一次清空的冲力大,清孔能力强,可以把绝大部分沉渣和较大的泥块都清除孔外,二第二次清孔是利用导管来进行的,冲力要小很多,不能让它来承担主要的清孔任务。如果第一次清孔能达到规定的沉渣厚度要求,第二次清孔作为储备,要保险很多。而每次施工结束后都清孔,同时又要保证孔壁的岩土层不再坍塌,在实际施工中很难做到这两者之间到理想的平衡状态,容易造成塌孔、缩颈等问题,进而将会不同程度地影响到施工的施工效率和质量。因此,在进行旋挖桩施工时,一定要按规定要求严格实施,控制好孔底的残留沙土,确保孔底的残留沙土不会影响到整个施工工程的质量。
广州越秀区某办公大楼,地上18层,地下2层,基坑开挖深度约14m。根据勘察资料,本场地基岩为红层,上覆残积土层、全/强风化泥质粉砂岩层厚度约为31m,以下为中/微风化泥质粉砂岩,设计要求桩入中/微风化岩深度1.0m,当时施工时采用的是旋挖桩。本工程桩基础施工完成后共抽芯检测8条桩,其中一条桩的两个检测钻孔分别发现的桩底沉渣厚度达到了207mm、189mm;另一条桩的两个检测钻孔分别发现的桩底沉渣厚度达到了55mm、57mm,其他桩也分别有厚度相对较小的沉渣,造成了较大的经济损失。
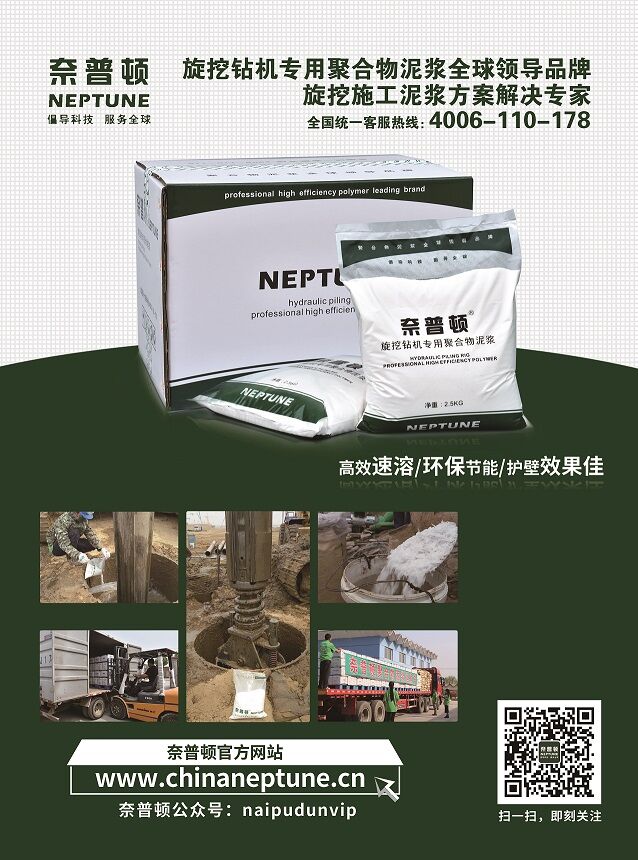
1、旋挖桩施工的特点
1.1成孔速度快
一般情况下,旋挖钻机的钻孔与成孔速度可以达到1-1.5m�min,与国内桩基础工程中传统的循环钻机相比,其优势极为明显。由于旋挖钻机的成孔速度快,在保证施工进度的基础上,有效减少了施工的人力、物力投入。
1.2适应性强
旋挖钻机采用液压履带式伸缩底盘、自行起落可折叠钻桅、伸缩式钻杆、带有垂直度自动检测、调整、孔深数码显示等。旋挖钻机配合不同钻具,适用于干式(短螺旋)或湿式(回转斗)及岩层(岩心钻)的成孔作业。旋挖钻机还可配挂长螺旋钻、地下连续墙抓斗、振动桩锤等,实现多功能特点,其施工效率高,是市政建设、铁路、公路桥梁、地下连续墙、水利、防渗护坡等理想的基础施工设备。旋挖钻机适用于填土层、粘土层、粉土层、淤泥层、沙土层以及短螺旋不能钻进的含有部分卵石、碎石的地层。采用岩心钻头,还可嵌入岩层。据国内机械技术部门研究,旋挖钻机的成孔速度是循环钻机的5-10倍之间。
1.3环保性能突出
国内传统循环钻机普遍采用连接钻杆与掏渣桶掏渣的泥浆循环方式,在施工现场必须设置一定容积的泥浆池,从而难以保证文明施工。而现阶段使用的旋挖钻机则是采用动力头的循环形式,其基本工作原理为:使用螺旋钻头与旋挖斗,通过强大的扭矩将土、砂砾等钻进中产生的钻渣直接进行旋挖挖掘,并快速提至孔外。由此可见,旋挖桩在施工中无需设置泥浆支护结构,实现了较为环保的干法施工,必然使施工作业过程的污染源明显减少,有利于改善施工现场的作业环境。
2 旋挖桩施工工艺流程
旋挖桩的施工工艺流程为:场地平整→孔位测定→埋设护筒→钻机就位→开钻成孔→提钻清空→检孔→安放钢筋笼→下导管→水下混凝土灌注→提拔导管→成桩→拔出护筒→检测。
3 旋挖桩施工出现的主要问题
3.1嵌岩能力差
旋挖钻机施工原理是利用可以伸缩的旋式钻杆在钻具重量、油缸压力及动力头扭矩的共同作用下,钻机自动定位,垂直旋孔,将地下土、岩屑装入钻头(筒),再用卷扬机提升取土(岩)成孔。配合不同钻具,可用于不同孔径及地质条件的成孔作业。这就决定了如果遇到硬度较大的基岩时,钻进难度就会明显加大。
广州某部队办公指挥大楼桩基础施工,根据勘察资料,该地区基岩为燕山期花岗岩。场地中风化岩面埋深32.9~45.2m,平均37.8m;层厚0.0~2.2m,平均1.2m;取岩样饱和单轴抗压强度范围值为7.38~39.6MPa,平均值为18.7MPa。下覆微风化花岗岩饱和单轴抗压强度范围值为42.2~86.5MPa,平均值为68.1MPa。设计要求桩入中/微风化岩0.5m。在桩的成孔方式上,相关单位考虑到工期及环保因素,决定采用旋挖桩成孔。试桩时,约用时1小时便穿过上部约35m厚的土层,在遇到硬度相对较大的中风化花岗岩时,钻进速度极剧下降,表现出明显的钻进困难。经多次反复旋挖,仍然没用明显的钻进效果。最终不得不停止旋挖,改用钻桩机成孔,造成了一定的经济损失并延误了工期。
广州地区基岩多为花岗岩和红层(泥质粉砂岩、粉砂质泥岩、泥岩等),在桩基础的选择上,相关单位应充分考虑到基岩的强度。如果采用嵌岩桩,在较硬的花岗岩地区,不建议采用旋挖桩;在较软的红层地区,则可采用旋挖桩,成孔速度较理想。
3.2桩底沉渣厚度大
当钻孔到达设计桩长以及进入持力层规定深度后,直接利用钻具进行换浆清孔工作,利用钻头叶片的搅动作用和泥浆对沉渣的浮力,将孔底沉渣排出孔外。清孔时应另行输入比重在1.1g/cm3以下的经沉淀除渣后较洁净的泥浆吗,逐步置换出孔内较粘稠、含较多泥砂的泥浆,而不直接输入清水,以防止发生孔壁坍塌。清孔后孔底500mm以内泥浆比重应小于1.25,含砂率不大于8%,粘度不大于28s。第一次清孔是能否达到技术要求的根本基础,第一次清空的冲力大,清孔能力强,可以把绝大部分沉渣和较大的泥块都清除孔外,二第二次清孔是利用导管来进行的,冲力要小很多,不能让它来承担主要的清孔任务。如果第一次清孔能达到规定的沉渣厚度要求,第二次清孔作为储备,要保险很多。而每次施工结束后都清孔,同时又要保证孔壁的岩土层不再坍塌,在实际施工中很难做到这两者之间到理想的平衡状态,容易造成塌孔、缩颈等问题,进而将会不同程度地影响到施工的施工效率和质量。因此,在进行旋挖桩施工时,一定要按规定要求严格实施,控制好孔底的残留沙土,确保孔底的残留沙土不会影响到整个施工工程的质量。
广州越秀区某办公大楼,地上18层,地下2层,基坑开挖深度约14m。根据勘察资料,本场地基岩为红层,上覆残积土层、全/强风化泥质粉砂岩层厚度约为31m,以下为中/微风化泥质粉砂岩,设计要求桩入中/微风化岩深度1.0m,当时施工时采用的是旋挖桩。本工程桩基础施工完成后共抽芯检测8条桩,其中一条桩的两个检测钻孔分别发现的桩底沉渣厚度达到了207mm、189mm;另一条桩的两个检测钻孔分别发现的桩底沉渣厚度达到了55mm、57mm,其他桩也分别有厚度相对较小的沉渣,造成了较大的经济损失。
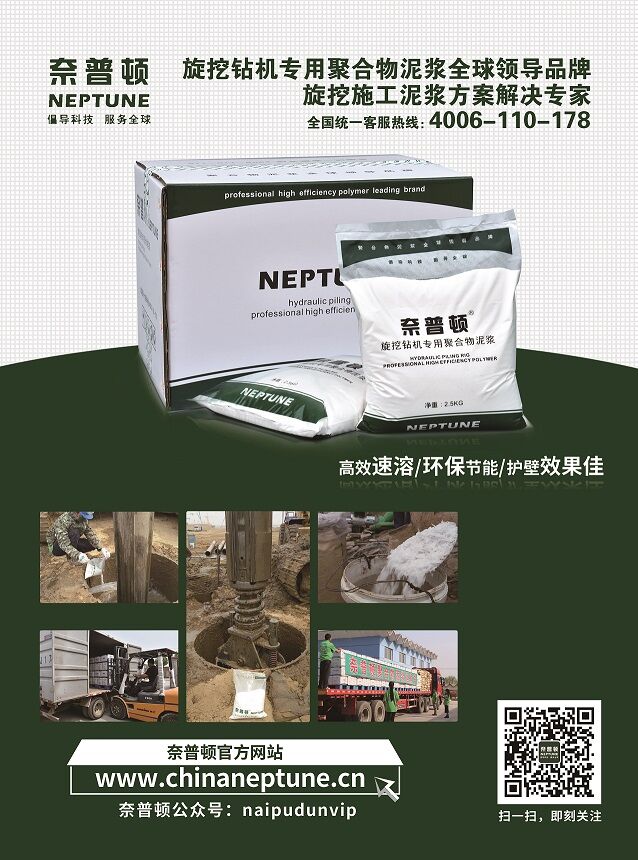
- 上一篇:旋挖扩底灌注桩施工工法 2018/11/9
- 下一篇:奈普顿聚合物泥浆网站新版进入调试阶段【公司新闻】 2012/5/23