工程简介
本工程桩基础采用钻(冲)孔灌注桩和人工挖孔桩两种桩型,共500根。场地目前部分区域基坑开挖到绝对标高34.00米左右,已具备桩基础进场施工条件。该工程工期较紧、地质较复杂场地部分区域存在淤泥质土层③-2和砂混淤泥层③-3,现基坑开挖面部分区域淤泥质土层外露,严重影响施工机械的正常施工和行走,土层及花岗岩风化层存在较多的花岗岩孤石,严重影响桩基的成孔施工,桩端进入微风化花岗岩层。地质复杂且微风化花岗岩单轴极限抗压强度约为100Map。
按勘探资料显示岩石力学性质参数统计表
层序号 岩性 统计组数(件) 抗压强度范围值(Mpa) 平均值(Mpa) 标准差(σ)变异系数(δ) 统计修正系数(γs) 标准值(Mpa)
⑤-3 中等风化花岗岩 1 28.9 / / / / /
⑤-4 微风化花岗岩 12 71.17~102.53 87.57 10.148 0.116 93.92 82.25
旋挖机的选用及入岩原理
1、入岩旋挖钻机介绍及原理
入岩旋挖钻机介绍:
旋挖钻机作为基础工程机械中的新型机种,经过几年的推广应用,目前已被大量应用于公路及铁路、桥梁、水利工程、城市建筑工程等桩基工程之中。由于其高效、节能、低噪声、低污染、地层适应性较广等优点、受到越来越多的施工单位的青睐。
而入岩旋挖钻机目前还为广泛使用,入岩旋挖机主机应具备的条件,从主机能力看,必须具备大的加压能力和大的动力头功率(大扭矩和高转速);从入岩工况看,设备本省必须具备较高的抗振动能力。现施工现场我司进的2台旋挖机均具备此两项条件,设备为山河智能25型及山河智能36型,其主要区别在于发动机大小、动力头扭矩大小等。
旋挖钻机技术参数对比
机型 SWDM36 SWDM25
整机重量 110t 72t
工作状态(长×宽×高) 10.5×4.8×25.6(m) 9.11×4.4×22.7(m)
运输状态(长×宽×高) 18.97×3.3×3.59(m) 16.6×3.0×3.4(m)
最大钻孔直径(带套管/不带套管) 2000/2500(mm) 1700/2200(mm)
最大钻孔深度(斗钻工法) 96(6节)/77(5节)(m) 72(5节)/57(4节)(m)
发动机
品牌 CUMMINS CUMMINS
型号 QSX15-C540-T2 QSL9-325
额定功率 403kW/2100rpm 242kW/2100rpm
最大扭矩 2360Nm/1400rpm 1424Nm/1500rpm
动力头
最大扭矩 3600kN.m 258kN.m
转速 6~24(rpm) 6~26(rpm)
加压系统
最大加压力 340kN 185kN
最大提升力 340kN 210kN
最大行程 17600mm 5000mm
主卷扬
最大提升力 360kN 260kN
最大提升速度 60m/min 51m/min
钢丝绳直径 40mm 32mm
副卷扬
最大提升力 110kN 80kN
最大提升速度 55m/min 55m/min
钢丝绳直径 24mm 20mm
底盘
最大行走速度 1.2km/h 3.5km/h
最大爬坡度 15° 15°
最小离地间隙 322mm 325mm
履带宽度 900mm 800mm
履带伸缩宽度 3300~4800(mm) 3000~4400(mm)
履带纵向轮距 5150mm 4700mm
平均接地比压 118.7kPa 95.7kPa
钻杆
标配磨阻式钻杆 D508-6×17.6m D470-5×15.5m
选配机锁式钻杆 D508-5×17.6m D470-4×15.5m
入岩旋挖钻机施工原理:
旋挖钻机入岩或处理孤石采用脆性剪切碎岩,其机理是在岩石颗粒边界处利用两向力即加压力和扭矩或多维应力共同作用产生搓碾剪切从而导致岩石破碎的一种准静载破岩方式。入岩的工效取决于钻具的选择,目前能入岩的钻具有:硬岩捞砂钻头、螺旋钻头、合金取芯钻头、滚刀嵌岩筒钻等,常用的碎岩工具均应具有点式或圆球形切削刃面。
流程简述:先用嵌岩筒钻钻进,嵌岩筒钻前部设置有滚刀钻头,能在坚硬岩石中取芯钻进,就像超前钻一样取芯,当入到孤石时可以整段取出来,如果孤石长度超过钻斗长度,如岩石能掰断则整段提出地面,如岩石断面掰不断则采用螺旋钻头将岩芯破碎,岩石破碎后用双底捞砂斗清除孔内岩渣。
嵌岩筒钻(钻头)螺旋钻头
双双底捞砂斗(钻头)旋挖机入岩钻进施工现场
现场取出的岩石芯样
旋挖钻机入岩成孔工艺流程
1测量放线定位:
场地三通一平后,复核建设单位提供的测量控制点符合要求后,测放出各桩桩位,拼装好桩架就位。根据预先测设的测量控制网(点),定出各桩位中心点。双向控制定位后埋设钢护筒并固定,以双向十字线控制桩中心。开钻前必须先校核钻头的中心是否与桩位中心重合。在施工过程中还须经常检测钻具位置有无发生变化,以保证孔位的正确。
2护筒埋设:
护筒直径大于钻头直径,并确保筒壁与水平面垂直,隔离地面水,稳定孔口土壤和保护孔壁不塌,以保证其垂直度并防止泥浆流失,以利钻孔工作进行。挖掘机开挖出护筒孔位,然后吊放入护筒,同时用十字线校正护筒中心及桩位中心,使之重合一致,护筒周围用粘土分层夯实。
3成孔:
在钻孔过程中要根据土层情况合理调节泥浆的比重,施工前应准备好泥浆粉或购买达到成孔要求的泥浆。桩位允许偏差50mm,桩身垂直度偏差不大于1/200,依据土层情况,控制钻进速度。成孔施工要以地质资料为指导,对于施工中出现的各种问题,要判断正确处理及时。桩端进入设计孔深后方可终孔验收,进入下道工序。
4泥浆系统及泥浆处理:
根据附属结构的分布范围,设泥浆池,泥浆池分别设置沉淀池、循环池、储浆池。
拌制泥浆选用膨润土,经分离处理后的废渣,通过密闭的专用汽车外运。施工中做到泥浆不外溢,严禁将废浆直接排入场地周边的下水道或河道。
5清孔
钻孔至预定深度后即可清孔。清孔采用循环出渣的方法,孔底沉渣厚度不应大于50mm,直至孔底泥浆的各项指标符合施工要求。
6钢筋笼制安:
6.1钢筋笼制作
进场钢筋有出厂证明或合格证,试验合格单,现场见证取样进行原材复试。
钢筋笼整段加工成型,钢筋接头采用搭接焊,单面焊10d,双面焊5d,d为钢筋直径。螺旋筋和加劲筋与主筋采用点焊,加劲筋接头采用单面焊10d。
钢筋笼成型后根据规范要求进行自检、隐检和交接检,内容包括钢筋(外观、品种、型号、规格)、焊缝(长度、宽度、厚度、咬口、表面平整等)、钢筋笼允许偏差(主筋间距、加劲筋间距、钢筋笼直径和长度等),并作好记录。结合钢筋焊接取样试验和钢筋原材复试结果,有关内容报请监理工程师检验,合格后方可吊装。
钢筋笼保护层厚度50mm,采用Ф10钢筋作为导向钢筋保护层,沿钢筋笼周长水平均布4个,纵向间距4m。
检验合格后的钢筋笼应按规格编号分层平放在平整的地面上,防止变形。吊装时由汽车吊吊由指定位置吊到钻孔桩孔旁,再进行吊装入孔。
6.2钢筋笼吊装
在下放过程中,吊放钢筋笼入孔时应对准孔位,保证垂直、轻放、慢放入孔。入孔后应徐徐下放,不得左右旋转,若遇障碍停止下放,查明原因进行处理,严禁高提猛落和强制下放。
6.3钢筋笼安装就位
以护筒周边硬质土面为基准面,量测钢筋笼长度,复核钢筋笼顶端到达设计标高,随后立即固定;下放钢筋笼时,要求有技术人员在场,使用Ф16吊筋以控制钢筋笼的桩顶标高;安装钢筋笼完毕到灌注混凝土时间间隔不应大于4小时。
7水下混凝土施工
7.1导管和漏斗
选择合适的导管,导管直径为250mm。导管组装时接头必须密合不漏水(要求加密封圈)。在第一次使用前应进行闭水打压试验,试水压力0.6-1.0MPa,不漏水为合格,导管底端下至孔底标高上500mm左右,漏斗安装在导管顶端。
7.2对混凝土的技术要求
桩设计要求混凝土强度为C30,坍落度180~220mm。采用普通硅酸盐水泥,可适当掺加高效减水剂,掺量根据试验确定,并经设计师的认可;不允许任何含有氯化钙的外加剂用在混凝土配合比中;配制的混凝土应该密实,具有良好的流动性;满足水下混凝土灌注并为保证设计要求,以保证桩身混凝土的强度。
7.3浇筑水下混凝土
(1)水下灌注混凝土必须具备良好的和易性,配合比应通过实验室试验确定;坍落度宜为180~220mm;水泥用量不应少于360kg/m3;浇筑前必须检查混凝土塌落度,记录并拍照,经监理检测合格后方可进行浇注;
(2)第一次浇筑混凝土时先将漏斗下部封住,灌满漏斗(约2m3)后用吊车拔出漏斗塞,使混凝土一次性浇筑到底,期间混凝土罐车持续浇筑,第一车混凝土浇筑完成后相对降低浇筑速度;
(3)导管埋入混凝土深度宜为2~6m。严禁将导管提出混凝土灌注面,并应控制提拔导管速度,应有专人测量导管埋深及管内外混凝土灌注面的高差;
(4)混凝土混凝土灌注过程中,始终保持导管位置居中,提升导管时应有专人指挥掌握,不使钢筋骨架倾斜、位移,如发现骨架上升时,立即停止提升导管,使导管降落,并轻轻摇动使之与骨架脱开。
混凝土灌注到桩孔上部5米以内时,可不再提升导管,直到灌注至设计标高后一次拔出,灌注至桩顶后必须多灌0.5m,以保证凿去浮浆后桩顶混凝土的强度。
混凝土灌注完成后及时拔出护筒,在最后一次拔管时,要缓慢提拔导管,以避免孔内上部泥浆压入桩中。
灌注混凝土过程中,及时测量混凝土面的标高,严格控制超灌高度,确保有效桩长和保证桩头的高度。
在灌注水下混凝土过程中,设泥浆泵及时排水防止泥浆漫出,确保文明施工。做好并收集、整理好各种施工原始记录,质量检查记录等原始资料,并做好施工日志。
施工参数
遇到孤石层或基岩采用嵌岩筒钻一开钻杆自身重量慢慢加压切入,待岩石切入有10mm左右采用液压加压强力切入,效果性非常明显。既可保证入岩,也保证成孔垂直度。使用该法入岩1天可完成3~4根桩(19m/根),每米微风化花岗岩约需施工4小时。
旋挖机与冲孔桩机入岩工效对比
冲孔桩机:3~4天完成1根(19m)桩,每米微风化花岗岩至少需施工1.5天;
入岩旋挖机:1天可完成3~4根桩(19m/根),每米微风化花岗岩约需施工4小时;
另外旋挖有助于安全文明施工:
冲孔桩机:移动缓慢,用电量大,作业占地较大(泥浆池较多),泥浆处理困难大,噪音大,不够环保。
无固相旋挖机泥浆:移动灵活,使用柴油,可损耗泥浆,噪音小,较环保。
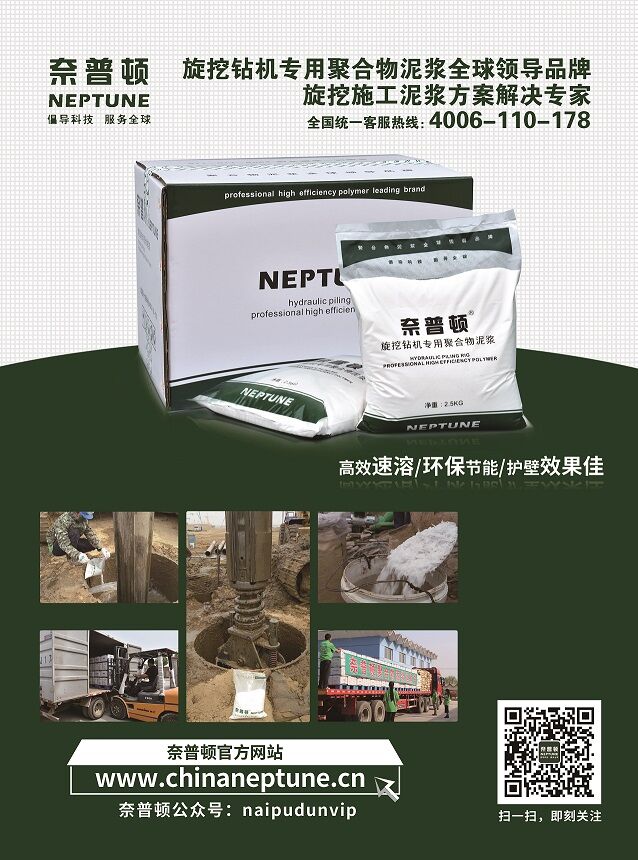